The Impact of Robots on the U.S. Labor Market
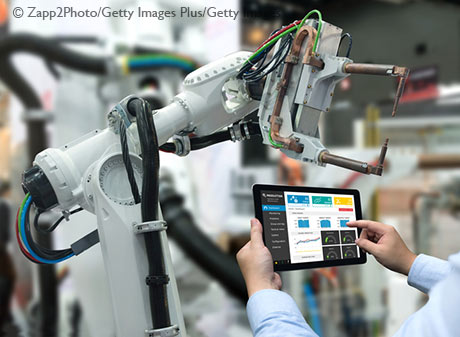
The following post is the second in a two-part series on the impact of robots on the workplace and the labor force.
In the previous post, St. Louis Fed Economist Maximiliano Dvorkin and Research Associate Asha Bharadwaj analyzed the growing use of industrial robots in advanced industrial economies. They discussed how the use is distributed among different industries.
The question that remains unanswered: How might the growth in robots affect local labor markets?
“For instance, some workers in the automotive industry, possibly those conducting more manual and routine tasks, may be experiencing job losses as more and more of these jobs are automated by the use of robots,” they wrote.
“On the other hand, it is also possible that robots raise overall productivity and efficiency, leading to an increase in the demand for other types of jobs that are more complementary to the use of robots, like technicians,” they continued.
The authors also noted that other industries may benefit from these productivity spillovers in the automotive industry and increase their own demand for labor.
Commuting Zones
As part of their analysis, they defined local labor markets as U.S. commuting zones rather than metropolitan statistical areas.
“A commuting zone can be defined as a geographic unit that combines counties into an area that reflects the concept of a local labor market better than a metropolitan statistical area does,” they said.
Dvorkin and Bharadwaj then constructed a measure for how exposed those U.S. commuting zones were to the rising number of robots used in production.
Using industry-level data from the International Federation of Robotics, and adjusting that data for industries’ workforces, they derived a way to show how exposed these commuting zones were to the increasing number of robots per thousand workers from 1990 to 2007. The figure below shows this exposure.
(For more on their methodology, see the Regional Economist article The Rise of Automation: How Robots May Impact the U.S. Labor Market.)
They observed that Rust Belt states such as Michigan, Ohio and Indiana saw a concentration of rising exposure to robots.
“This result is not surprising. Rust Belt states have a large concentration of employment in the automotive industry, along with other manufacturing, and thus the exposure to robots is more pronounced,” they wrote.
For these states, the increases ranged between 3.14 and 15.47 adjusted robots per thousand workers in many of the region’s zones, the authors wrote.
On the other extreme were several states—such as those in the Great Plains and the Rocky Mountains—where exposure has been more limited. In many of those states’ commuting zones, increases ranged between 0.13 and 0.80 adjusted robots per thousand workers.
“How does this heterogeneity in the penetration of robots at the level of industry and geography translate into labor market effects?” Dvorkin and Bharadwaj asked. To answer that question, they dug into the relationship between this exposure measure and labor market outcomes.
The authors looked at the change of the employment-to-population ratio of one job type, which they called “routine manual.” (The routine manual classification includes construction, transportation, production and repair occupations.) They examined the change for more than 700 U.S. commuting zones, and how that change might be linked to the zone’s exposure to robots from 1990 to 2007. (See figure below.)
The scatterplot implies that an increase in the exposure to robots by one unit per thousand workers is associated with a decline in the commuting zone’s ratio of routine manual employment to population by around 0.12 percentage points, according to their analysis.
“In other words, the analysis suggests that the larger increase in the use of robots in some commuting zones may be reducing the number of people employed in routine manual occupations relative to population in those commuting zones,” the authors wrote.
However, they cautioned against drawing too much from that correlation: The figure above may paint a negative picture at first blush, but the authors said that from this figure alone, they cannot “pin down” the aggregate effects of automation on employment.
“It may be possible that automation leads to an overall increase in employment, with the increase being lower in commuting zones with higher exposure to robots due to relatively fewer routine manual jobs,” they wrote.
Further research would be needed, they said.
Automation as a Driver of Polarization
Still, Dvorkin and Bharadwaj noted that their analysis revealed a negative relationship between automation and routine manual employment in local labor markets, which supports the thesis that automation may be an important driver of polarization in the labor market.
This polarization already is seen in “the decline of middle-skill occupations, like manufacturing and production jobs, and the growth in both high- and low-skill occupations, like managerial jobs on one end and jobs that assist or care for others on the other,” they wrote.
The authors concluded that though they focused on robots and routine manual jobs, the broader wave of automation is expanding to other jobs.
For example, advances in artificial intelligence and computerization have allowed certain cognitive work, such as handwriting recognition and pretrial research, to become automated to a certain extent.
“Other cognitive skills, such as decision-making under challenging situations in intensive care units (ICUs), may soon be supplemented by algorithmic recommendations,” they wrote. “Thus, automation can have far-reaching consequences that may lead to structural shifts in the labor market.”
Additional Resources
- On the Economy: The Rise of Robots in the Workplace
- On the Economy: Most Jobs Face Automation in Next 20 Years
Citation
ldquoThe Impact of Robots on the U.S. Labor Market,rdquo St. Louis Fed On the Economy, Nov. 5, 2019.
This blog offers commentary, analysis and data from our economists and experts. Views expressed are not necessarily those of the St. Louis Fed or Federal Reserve System.
Email Us
All other blog-related questions