The Rise of Automation: How Robots May Impact the U.S. Labor Market
KEY TAKEAWAYS
- Industrial robots are a type of automation technology that could lead to a structural shift in the labor market, particularly among routine manual jobs.
- The use of robots has expanded globally. In the U.S., there were 1.79 robots per thousand workers in 2017, up from 0.49 robots per thousand workers in 1995.
- An analysis of data suggests that more robots in a U.S. commuting zone may reduce the number of workers in routine manual jobs relative to the zone’s population.
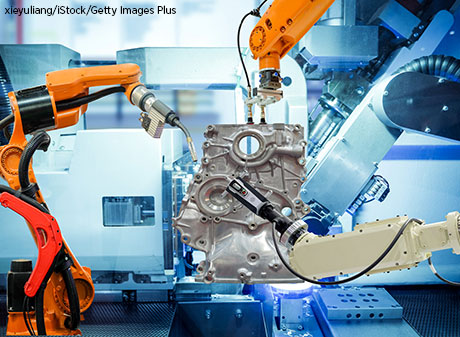
An important long-run change in U.S. labor markets is the decline of middle-skill occupations, like manufacturing and production jobs, and the growth in both high- and low-skill occupations, like managerial jobs on one end and jobs that assist or care for others on the other. Economists have coined the term “job polarization” for this process.See, for example, Goos et al., Autor et al., and Autor and Dorn.
As has been argued in the economic literature, the most likely drivers of job polarization are automation and offshoring, because both these forces lower the demand for middle-skill occupations relative to the rest. Automation refers to any technology that reduces the need for human assistance. For instance, processes such as grocery store checkout have been automated to a great degree and thus require less labor to perform routine tasks. Similarly, some stages of the production process of a good or service can be performed in foreign countries; therefore, certain tasks can be outsourced. In general, the types of tasks that can be outsourced are mostly routine tasks.
In this article, we focus on industrial robots, which are a specific type of automation technology. The International Federation of Robotics (IFR) defines an industrial robot as an “automatically controlled, reprogrammable [and] multipurpose manipulator, programmable in three or more axes, which can be either fixed in place or mobile for use in industrial automation applications.”See International Federation of Robotics. In other words, industrial robots are fully autonomous machines that do not require any human intervention and can be reprogrammed to perform several manual tasks. For instance, technologies like tractors or elevators are not industrial robots since they are able to perform only specific tasks and require some degree of human intervention.
Several economists believe automation represents a wave of technological change that could lead to a structural shift in the labor market. History suggests that this belief is well founded. In the early 19th century, the first industrial revolution was characterized by the development of the steam engine and the water wheel, and it changed the nature of the economy from being agrarian to urban. The second wave of technological change was marked by the increasing adoption of electricity by industries and technological advances such as the telephone and the internal combustion engine. The third industrial revolution was characterized by digitalization and the adoption of computers and the internet, and it changed the way in which information was transmitted and shared. Nowadays, the growth of automation and similar technological advances continue to accelerate, and many believe that the fourth industrial revolution has already begun.
In this article, we look closely at the link between industrial robots and employment in routine manual occupations. In a series of recent academic articles, economists Daron Acemoglu and Pascual Restrepo have studied the effects of the rapid increase in the use of manufacturing robots on the labor market, and we follow these works very closely in our analysis here.See, for example, Acemoglu and Restrepo, 2018 and 2019.
The Decline in Routine Jobs
Given the previous discussion, it is important to classify occupations according to the routine content. In addition, we also distinguish between occupations based on whether an occupation uses mostly cognitive skills or manual skills (brain vs. brawn).
Figure 1 shows the evolution of U.S. employment across different types of occupations:We follow Foote and Ryan in our classification of occupations into four broad groups.
- Nonroutine cognitive, which includes management, professional and related occupations
- Nonroutine manual, which includes service occupations related to assisting or caring for others, such as health care support, food preparation and serving, and cleaning
- Routine cognitive, which includes sales and office occupations
- Routine manual, which includes construction, transportation, production and repair occupationsWe exclude from this analysis farming, fishing, forestry and military occupations.
The picture is clear: Employment in nonroutine occupations, both cognitive and manual, has been increasing steadily for several decades, while employment in routine occupations has been mostly stagnant or even declining.
Adoption of Industrial Robots
We start by analyzing the evolution of the adoption of robots in the production of goods and services around the world. For this, we use data from IFR, which publishes data on the stock of robots by country, industry and year. The IFR data are based on surveys of robot suppliers and, as we said before, define an industrial robot as an automatically controlled, reprogrammable and multipurpose manipulator for use in industrial automation applications.
Figure 2 presents the evolution of the stock of industrial robots per thousand workers for a group of advanced economies around the world: the U.S., Germany, Italy, France, and an average for Spain, the U.K. and Sweden. These countries had the highest stock of industrial robots in 2017, and we grouped the bottom three—Spain, the U.K. and Sweden—to make the figure more readable.
We highlight two important facts from the data. First of all, there has been an important increase in the use of robots around the world, which in most cases has more than doubled in the last 20 years. The U.S. had a stock of 0.49 robots per thousand workers in 1995, which rose to 1.79 robots per thousand workers in 2017.
Second, we found that Germany and Italy are ahead of the U.S. in terms of adoption of robot technology in production, as measured relative to employment. France and the average of the countries Spain, the U.K. and Sweden were ahead of the U.S. in the late 1990s and early 2000s, but in the last decade, it seems that the U.S. has overtaken these countries.
This massive growth in the use of robots worldwide, particularly in the U.S., has motivated Acemoglu and Restrepo—and more recently, other economists—to investigate robots’ impact on U.S. labor markets.
Adoption of Robots across Industries
An important question arises: Is the use of robots uniform across industries? If not, is there a specific industry that is driving the adoption of robots?
Figure 3 highlights the use of robots in the automotive industry relative to the use of robots in all other manufacturing industries, as a share of employment in the respective industry.
Clearly, the automotive industry is by far the largest user of robots, in the U.S. as well as in other advanced countries around the world. For instance, in 2014, the automotive industry accounted for around 54% of the total U.S. stock of robots. For Germany, the share was higher, at around 60%.
From Figure 3, we observe that in all the countries shown, the ratio of robots to workers in the auto industry is far greater than the ratio of robots to workers in all other manufacturing industries combined. For instance, the U.S. auto industry employed 136 robots per thousand workers, while all other manufacturing industries in the U.S. employed only 8.6 robots per thousand workers. Similarly, France’s auto industry employed nearly 148 robots per thousand workers, while the rest of the manufacturing sector employed 5.5 robots per thousand workers.
The Link between Robots and Local Labor Markets
So far, we showed that there has been a rapid increase in the use of robots for production and that, as the previous figure suggests, this increase has not been uniform across different industries and, thus, across different types of workers.
Therefore, we now look closely at the asymmetric effects across labor markets. Several outcomes are possible. For instance, some workers in the automotive industry, possibly those conducting more manual and routine tasks, may be experiencing job losses as more and more of these jobs are automated by the use of robots. On the other hand, it is also possible that robots raise overall productivity and efficiency, leading to an increase in the demand for other types of jobs that are more complementary to the use of robots, like technicians. In addition, it is also possible that other industries benefit from these productivity spillovers and in turn increase their own demand for labor.
To study these effects more closely, we turn to local labor markets in the U.S. For this, we use the concept of a commuting zone and relate this to a local labor market. A commuting zone can be defined as a geographic unit that combines counties into an area that reflects the concept of a local labor market better than a metropolitan statistical area does.
We followed Acemoglu and Restrepo’s methodology (2019) and constructed a measure for commuting zones’ exposure to the increase in robots employed in production. To do this, for each industry and for each commuting zone, we divided the change in the stock of robots between 2004 and 2007 by the number of people employed in that industry in 1990. We then adjusted this term for the overall growth of production in each industry, and the results gave us the number of adjusted robots per thousand workers for each commuting zone.
We then weighted this by the baseline employment level in that commuting zone in the year 1990, which is the start of the period that we analyze. This gives us a measure for the exposure of a commuting zone to the increase in robots employed in production.
The International Federation of Robotics has data for 13 industries within manufacturing and for six broad sectors outside of manufacturing. Within manufacturing, we have data on apparel and textiles; automotive; basic metals; clay, glass and minerals; electronics; food and beverages; industrial machinery; metal products; paper and publishing; plastics, chemicals and pharmaceuticals; shipbuilding and aerospace; wood and furniture; and a miscellaneous manufacturing category. Outside of manufacturing, we have data for agriculture, construction, mining, research and education, services, and utilities.
Industry-level data for the U.S. are available starting in 2004, which is why our measure for the exposure to robots uses the change in the stock of robots between 2004 and 2007. We rescaled our measure of exposure to robots to match the length of the time period on which we focused (1990-2007). We ended our analysis in 2007 to prevent the effects of the Great Recession from confounding our results.
Figure 4 shows the map of U.S. commuting zones and their growing exposure to robots and automation in production. We observe that there is a concentration of rising exposure to robots in Rust Belt states such as Michigan, Ohio and Indiana. This result is not surprising. Rust Belt states have a large concentration of employment in the automotive industry, along with other manufacturing, and thus the exposure to robots is more pronounced, with increases ranging between 3.14 and 15.47 adjusted robots per thousand workers in many of the region’s zones. On the other hand, in several states, such as those in the Great Plains and the Rocky Mountains, the exposure has been more limited, with increases ranging between 0.13 and 0.80 adjusted robots per thousand workers in many zones of those states.
How does this heterogeneity in the penetration of robots at the level of industry and geography translate into labor market effects? To answer this question, we studied the relationship between this exposure measure and labor market outcomes. In particular, we focused on the change in the employment-to-population ratio of routine manual employment between 1990 and 2007 for 722 commuting zones in the United States and how this change may be linked to the exposure to robots. We used data on industry employment and production from the U.S. Bureau of Labor Statistics.
Figure 5 shows the scatterplot of these two variables, with the regression line represented by the solid black line. Each bubble in the graph is a single U.S. commuting zone, which we link to a local labor market, and the bubble’s size represents the size of the commuting zone in terms of employment in 1990.
The regression line shows a negative relationship between these variables, which implies that an increase in the exposure to robots by one unit per thousand workers is associated with a decline in the commuting zone’s ratio of routine manual employment to population by around 0.12 percentage points.Our strategy differs from Acemoglu and Restrepo’s in that they use the exposure to robots constructed from European data as an instrument for U.S. exposure, while we adopt a slightly simpler approach and directly use our measure for U.S. exposure in our analysis. If instead we were to follow Acemoglu and Restrepo’s methodology using instrumental variables, our results would be similar to the ones in their paper, except that we use a different measure of employment changes, that is, routine manual employment. In other words, the analysis suggests that the larger increase in the use of robots in some commuting zones may be reducing the number of people employed in routine manual occupations relative to population in those commuting zones.
While the figure may paint a negative picture at first glance, it is important to highlight that from this figure alone we cannot pin down the aggregate effects of automation on employment. It may be possible that automation leads to an overall increase in employment, with the increase being lower in commuting zones with higher exposure to robots due to relatively fewer routine manual jobs. To be able to estimate the overall effects of increased automation and the increased use of industrial robots, we need to complement this analysis with additional information or an alternative methodology, which is beyond the scope of this article.
Conclusion
Employment in routine occupations has been constant or declining over the past few decades, and automation is believed to be one of the reasons for this structural shift in the labor market. The use of robots in production has been steadily increasing since the early 1990s in most advanced economies around the world, and we used a unique dataset with information on the stock of industrial robots at the level of industries to construct a measure for a commuting zone’s exposure to robots.
Our analysis revealed a negative relationship between automation and routine manual employment in local labor markets, which supports the thesis that automation may be an important driver of polarization in the labor market.
While we focused on routine manual occupations in this article, automation could have an impact on a broader set of jobs. With advances in artificial intelligence and computerization, there are several cognitive skills, such as handwriting recognition and pretrial research, that already have been automated to a certain extent. Other cognitive skills, such as decision-making under challenging situations in intensive care units (ICUs), may soon be supplemented by algorithmic recommendations.See Frey and Osborne. Thus, automation can have far-reaching consequences that may lead to structural shifts in the labor market.
Endnotes
- See, for example, Goos et al., Autor et al., and Autor and Dorn.
- See International Federation of Robotics.
- See, for example, Acemoglu and Restrepo, 2018 and 2019.
- We follow Foote and Ryan in our classification of occupations into four broad groups.
- We exclude from this analysis farming, fishing, forestry and military occupations.
- Our strategy differs from Acemoglu and Restrepo’s in that they use the exposure to robots constructed from European data as an instrument for U.S. exposure, while we adopt a slightly simpler approach and directly use our measure for U.S. exposure in our analysis. If instead we were to follow Acemoglu and Restrepo’s methodology using instrumental variables, our results would be similar to the ones in their paper, except that we use a different measure of employment changes, that is, routine manual employment.
- See Frey and Osborne.
References
Acemoglu, Daron; and Restrepo, Pascual. “The Race between Man and Machine: Implications of Technology for Growth, Factor Shares, and Employment.” American Economic Review, June 2018, Vol. 108, No. 6, pp. 1488-542.
Autor, David H.; and Dorn, David. “The Growth of Low-Skill Service Jobs and the Polarization of the U.S. Labor Market.” American Economic Review, August 2013, Vol. 103, No. 5, pp. 1553-97.
Autor, David H.; Katz, Lawrence F.; and Kearney, Melissa S. “The Polarization of the U.S. Labor Market.” American Economic Review, May 2006, Vol. 96, No. 2, pp. 189-94.
Foote, Christopher L.; and Ryan, Richard W. “Labor Market Polarization over the Business Cycle,” in Jonathan A. Parker and Michael Woodford, eds., NBER Macroeconomics Annual 2014. Volume 29. Chicago: University of Chicago Press, 2015, pp. 371-413.
Frey, Carl Benedikt; and Osborne, Michael A. “The Future of Employment: How Susceptible Are Jobs to Computerisation?” Technological Forecasting and Social Change, January 2017, Vol. 114, pp. 254-80.
Goos, Maarten; Manning, Alan; and Salomons, Anna. “Job Polarization in Europe.” American Economic Review, May 2009, Vol. 99, No. 2, pp. 58-63.
International Federation of Robotics. World Robotics: Industrial Robots. 2018.
Views expressed in Regional Economist are not necessarily those of the St. Louis Fed or Federal Reserve System.
For the latest insights from our economists and other St. Louis Fed experts, visit On the Economy and subscribe.
Email Us